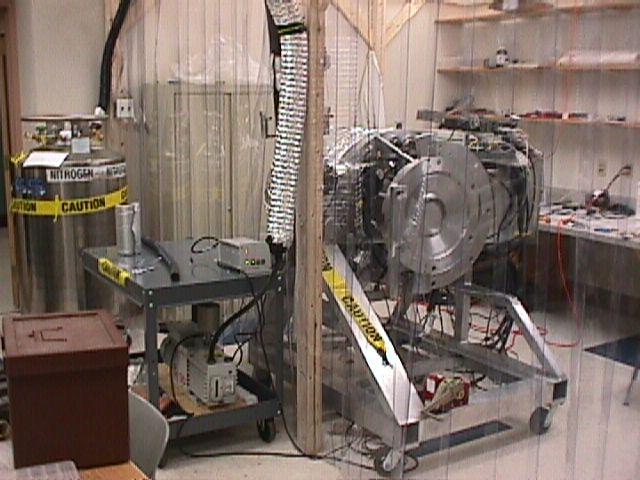 |
Lab configuration
for first cold test. The Mimir cryostat and stand reside within the
"biodome", our homemade clean room. It consisted of a fully
enclosed space with filtered positive pressure ventilation and overlapping
plastic curtain pieces in front. The LN2 storage dewar is at left,
vacuum pumping system at lower center. |
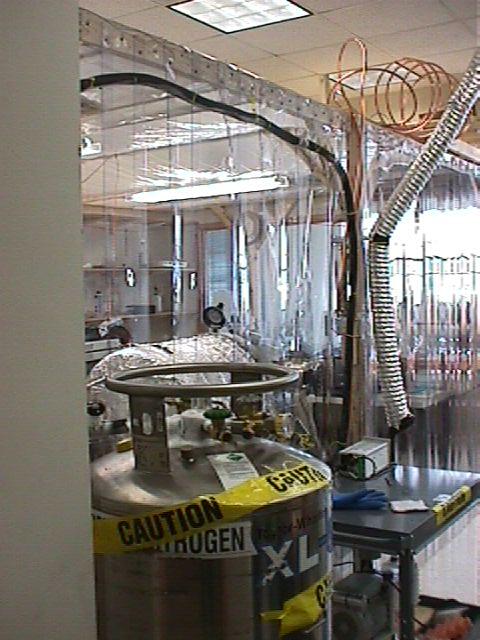 |
View of lab
from lab entrance door. The copper piping loops atop the biodome/cleanroom
are where the N2 exit gas is warmed back to room temperature before
being introduced into the flow gauges. Cryostat shell has heater
tape surrounded by aluminum foil.
Black tubing
across top front of clean room is the insulating jacket surrounding
the copper pipe that connects the LN2 storage dewar to Mimir's LN2
loop inlet.
During this
cooldown, we quickly discovered that this LN2 piping system was
very inefficient at delivering LN2 to Mimir. The pipe was shortened
to about 1 meter and the insulation tripled and MLI wrapped to reduce
heat intake and LN2 boiling prior to intake by Mimir.
|
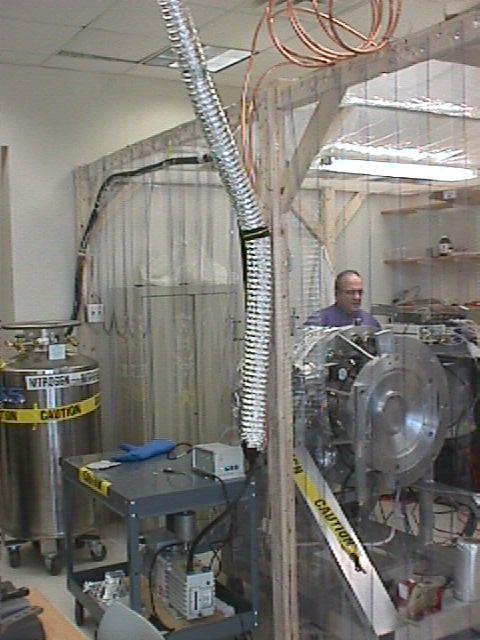 |
Domenic Sarcia
inspecting temperature sensor readings during cooldown. |
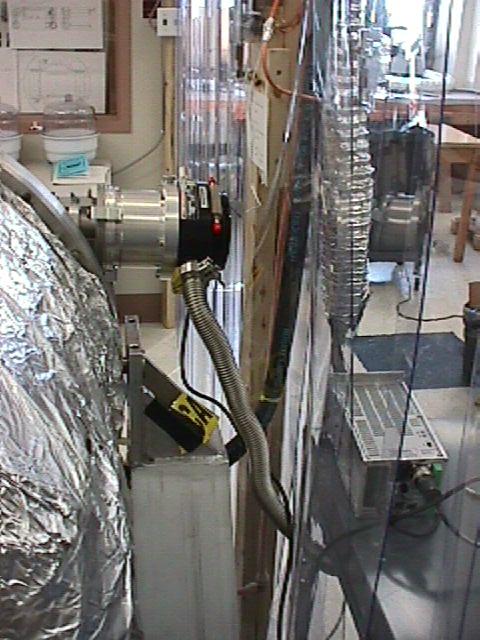 |
Turbo vacuum
pump mounted on side of Mimir (actually mounted directly to valve). |
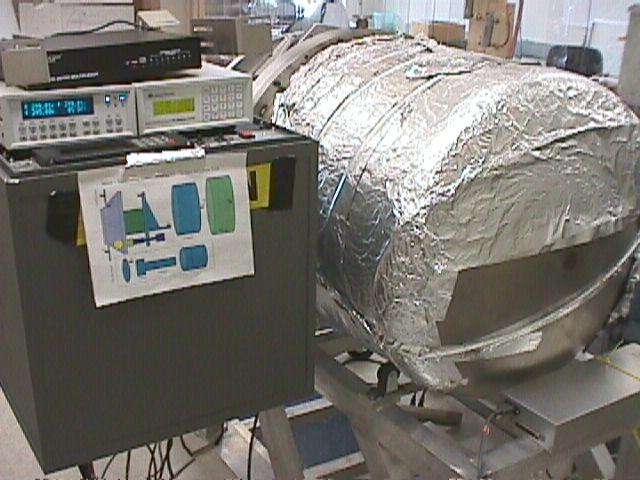 |
Rear view of
cryostat and sensor readouts during cooldown. Cartoon taped to electronics
box shows the internal locations of the various temperature sensors. |
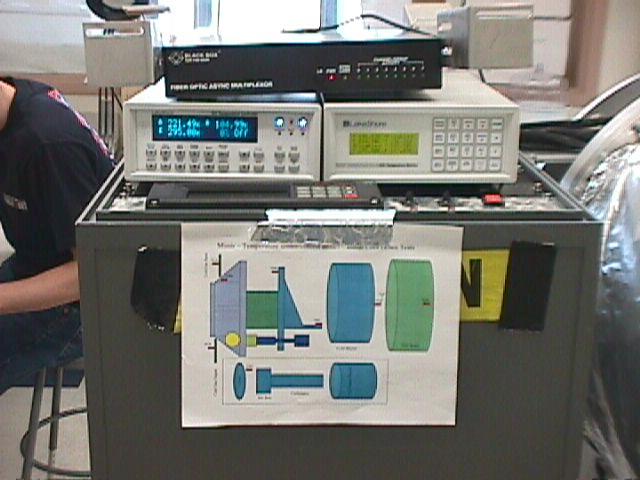 |
Closer view of
sensor location cartoon. Atop it, at left is the LakeShore LS331 temperature
controller and at right is the LS218 temperature monitor. Fiber multiplexer
is at top. |
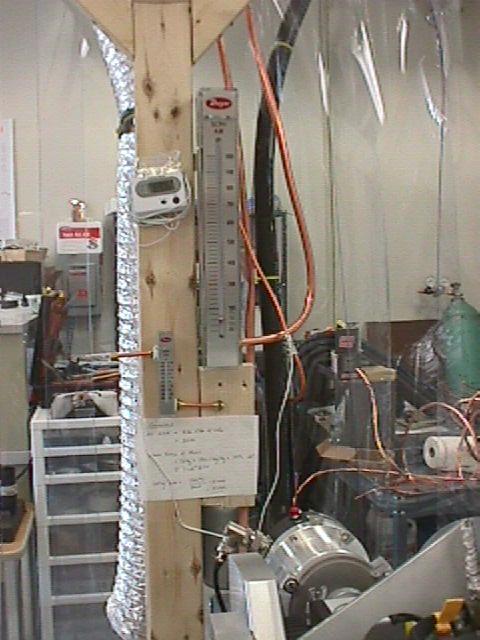 |
N2 flow gauge
during cooldown. Note that the indicating ball is in the lowest range
of the flow meter. |
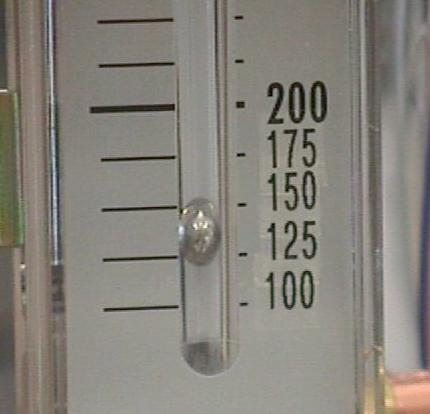 |
Zoomed view of
flow meter during cooldown, showing a flow rate of about 135 standard
cubic feet per hour (SCFH). |
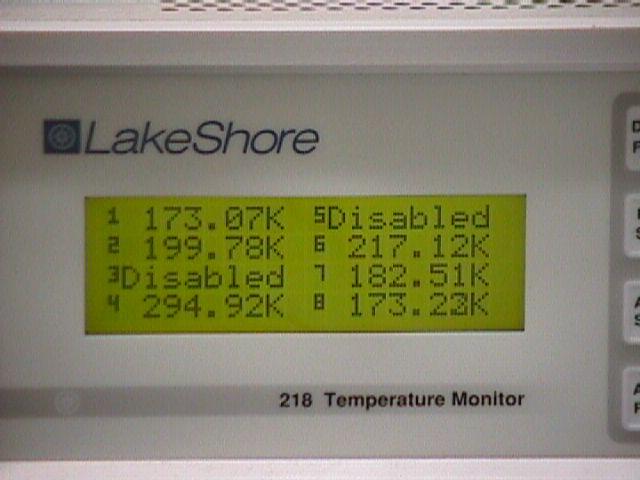 |
LS218 temperature
monitor readout during cooldown. |
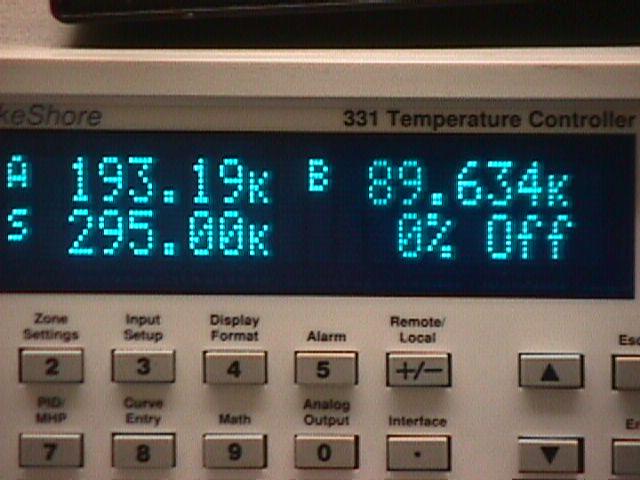 |
LS331 temperature
controller during cooldown. Sensor B and A report the temperatures
of the LN2 precool loop inlet and outlet, respectively. |
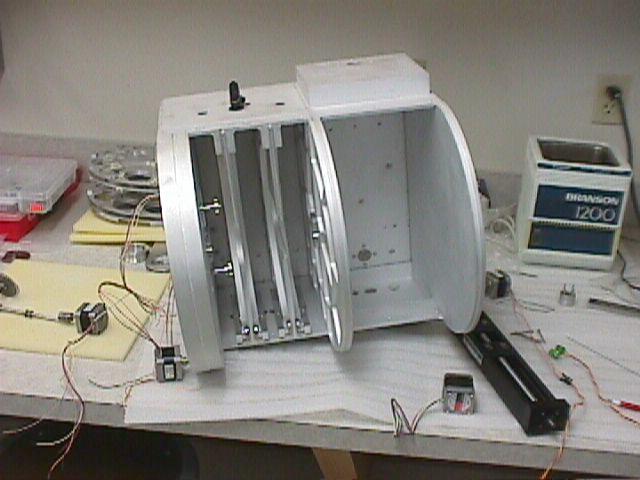 |
Filter Box with
motors on bench. Note THK screw drive unit at right (to be installed
as the camera drive unit) and filter wheel stack at upper left behind
filter box. |
 |
Setup for testing
stepper motors in liquid nitrogen. Dewar with LN2 at center, stepper
motor controller atop. Power supply at left, computer for commanding
stepper controller at right. |
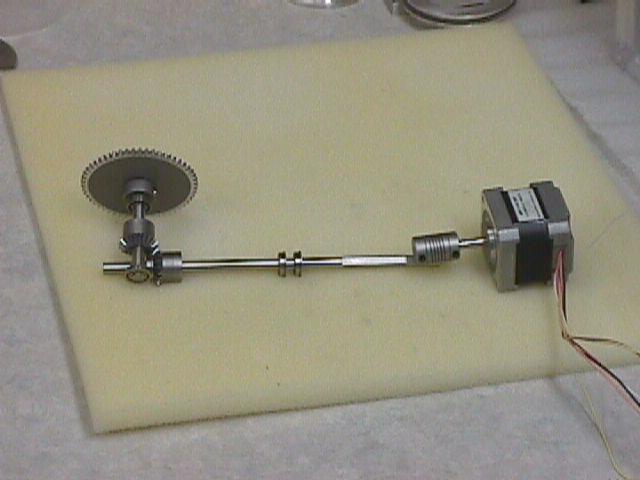 |
Gear drive system
for half-wave-plate rotation, consisting of a stepper motor with flex
coupling, drive shaft with twin bearing races, right angle gear drive,
second shaft with twin bearing races, and HWP filter cell drive gear.
This system is installed inside the filter box below the filter wheel
stack. |
 |
Test stand and
stepper controller for LN2 plunge testing of stepper motors. The aluminum
can is a short dewar filled with LN2. Inside, the motor being tested
is mounted on G10 standoffs. The motor shaft is attached to a longer
G10 shaft that exits through the center of the gray plate. The motor's
operation and stalling force can be seen and probed using the extension
shaft. |
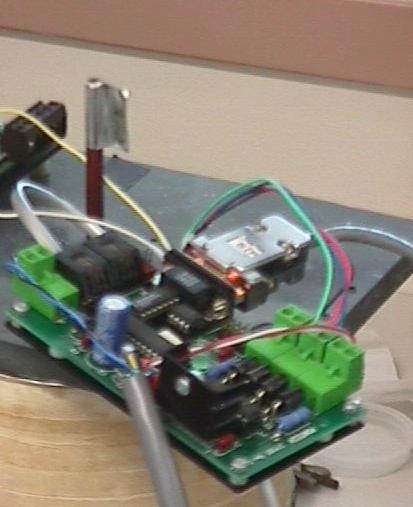 |
The rotatinng
aluminum "flag" attached to the brown shaft provides direct
visual verification that the stepper motor is working while surrounded
by LN2. |