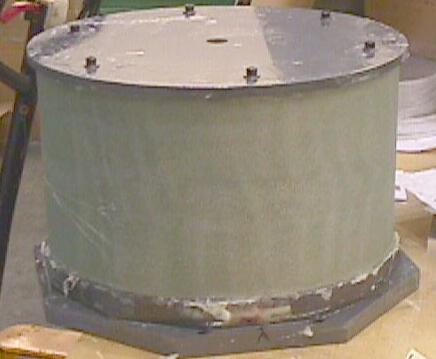 |
G10 collar on molding before machining. |
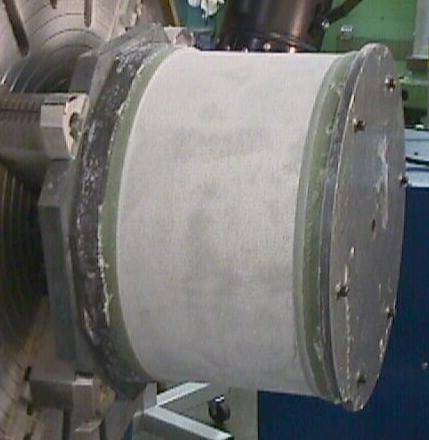 |
G10 collar on lathe. Outer diameter was turned down,
then lightly painted with a thin epoxy layer. The design length of
the G10 collar was cut and finished with the lathe and the collar
released from the mold. |
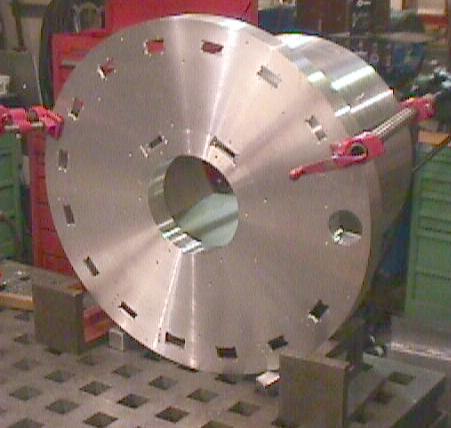 |
The cold mass within Mimir is all anchored to the cold
bulkhead, shown here, and the cold bench, held by two clamps to the
bulkhead in this picture. The assembly is being prepared for welding. |
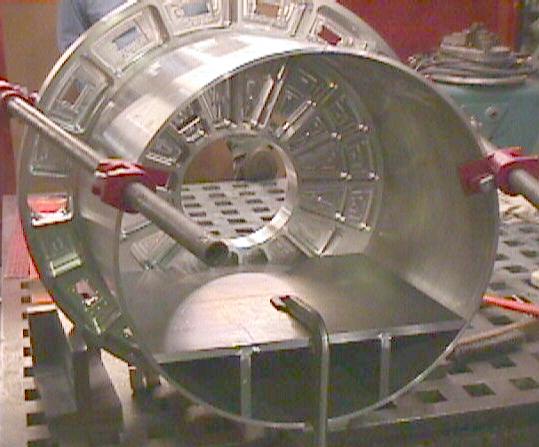 |
Rear view of cold bench and bulkhead. The bench is the
horizontal plate supported by three vertical gussets and the outer
cylinder. The cylinder is welded to the bulkhead, the bench welded
to the cylinder and bulkhead. After welding the sides of the cylinder
were cut down to retain stiffness with the smallest mass. |
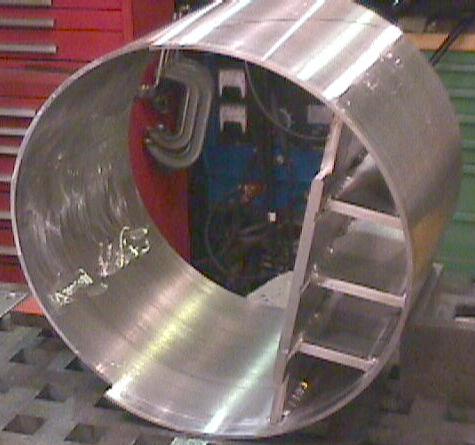 |
Cylinder and cold bench after their welding. |
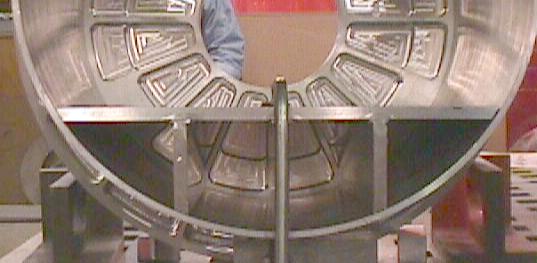 |
Rear view of cold bench and lightweighted bulkhead. |
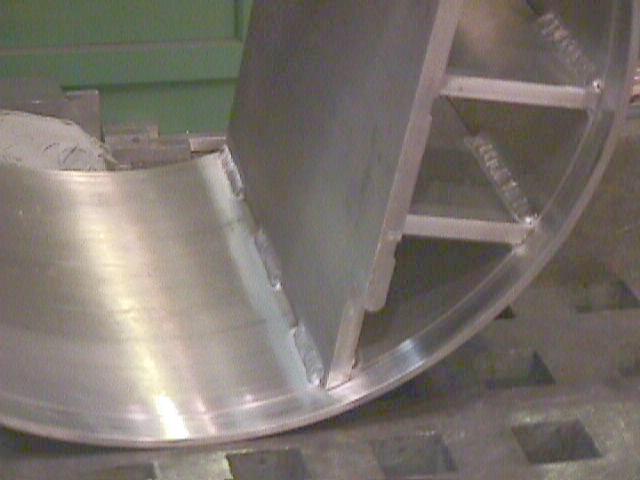 |
Cold bench and gussets weld detail. |
 |
Cold bench slides into pockets on the cold bulkhead
prior to welding. |
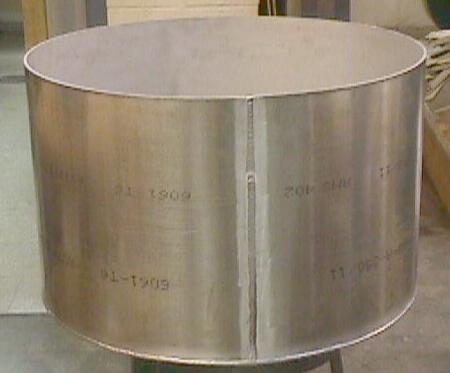 |
Active internal cold shield. This large cylinder bolts
to the outer part of the cold bulkhead to form a light tight cover
around the cold optics. This was fabricated at the shop as a welded
roll-up. |
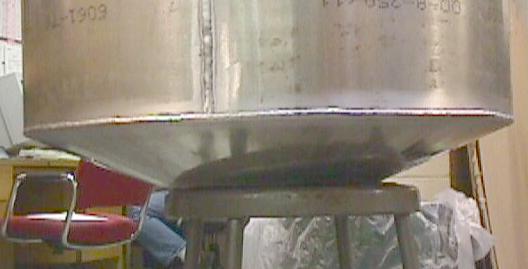 |
Tail piece of cold shield, sitting on lab stool. All
aluminum welds were made by Bob Kingsland of the BU shop. |